The Latest on Additive Manufacturing in Hypersonics
Add bookmark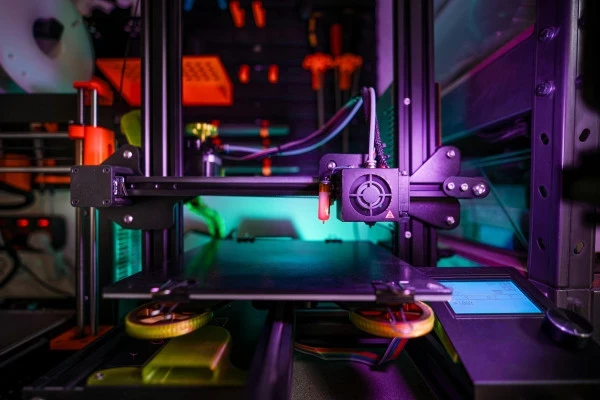
Hypersonic missiles have become the next step in the evolution of ballistics for militaries around the world. Traveling speeds at greater than match 5, and highly maneuverable and difficult to intercept, hypersonic missiles are proving to be more effective than traditional missiles. These missiles can be used in a variety of applications, including anti-ship, anti-aircraft, and anti-missile roles, as well as for delivering conventional and nuclear payloads.
Significant funding is being channeled into hypersonic missile technology. The Pentagon's FY2023 budget request for hypersonic research was $4.7 billion—up from $3.8 billion in the FY2022 request. In FY2024 the Pentagon requested $11 billion for long-range missiles, which includes hypersonic weapons.
Despite the potential effectiveness and uses of hypersonic missiles, the manufacturing process can be complex and requires advanced technologies and materials which leads to higher costs and long lead times. To overcome these challenges many organizations are turning to additive manufacturing and precision machining (such as 3D printing). These techniques can reduce costs and lead times by allowing for the production of complex parts and components in a single step.
DoD Efforts to Establish Additive Manufacturing Principles
The DoD has made it clear that additive manufacturing is one of their priorities when it comes to the development of hypersonic weapons. Keith DeVries, deputy director of the Office of the Secretary of Defense’s Manufacturing Technology Program, told Defense News in the summer of 2023 that hypersonic systems are a great example of a program where additive manufacturing can be used.
“Being able to incorporate additive manufacturing is enabling us to manufacture complexity that has not been able under the subtractive, traditional manufacturing methods,” DeVries said.
In the 2023 fiscal year the DoD launched an initiative called Growing Additive Manufacturing Maturity for Airbreathing Hypersonics, or GAMMA-H,with the goal of identifying materials and processes capable of building systems that travel at speeds beyond Mach 5.
This May, Aerojet Rocketdyne was awarded a $22 million Other Transaction Agreement (OTA) by the DoD to develop a prototype solution for the GAMMA-H challenge. Aerojet’s mission is to revolutionize the traditional scramjet manufacturing process using advanced manufacturing techniques.
“Aerojet Rocketdyne will consolidate several essential steps of the end-to-end scramjet manufacturing process under the GAMMA-H contract, which will provide schedule and cost efficiencies associated with a less fragmented supply chain,” said Aerojet Rocketdyne President Ross Niebergall. “Optimizing processes will increase part yields and reduce the number of processing steps, resulting in higher production velocity and lower cost.”
Examples of Additive Manufacturing in Hypersonics
Colleges and universities across the U.S. are playing a significant role in understanding the benefits additive manufacturing plays in developing hypersonics.
For example, a team at Purdue University’s Applied Research Institute (PARI) is using additive manufacturing to print a fully operational prototype of a supersonic combustion ramjet, a propulsion system enabling aircrafts to travel speeds beyond Mach 5.
This endeavour, conducted within PARI's Hypersonic Advanced Manufacturing Technology Center (HAMTC), aims to streamline prototyping and manufacturing processes for the hypersonics industry. The scramjet's design challenges lie in sustaining combustion at high velocities, similar to lighting a candle in a hurricane.
Despite the challenges of creating this powerful engine, researchers at PARI found the GE Concept Laser X Line 2000R, a printer used for large-scale manufacturing purposes, was capable of maintaining the necessary weight and desired part reduction without compromising functionality and geometric complexity needed for the engine to work.
The X Line 2000R printer deploys a technique called laser-powered bed fusion, a process where the laser in the printer melts and fuses together particles to form a solid part.
Similarly, at the Texas A&M Engineering Experiment Station researchers are working to bring additive manufacturing to the propulsion systems of hypersonic engines.
“3D-printing technology allows us to bypass the constraints of traditional manufacturing processes,” said Sabrina Ames, mission program manager at Ursa Major. “With additive technology, we can produce higher-performing fuel injectors and make fluid passages that mix fuel and oxidizer much more efficiently without adding significant mass to the parts.”
Besides Purdue and Texas A&M, other schools that are leaders in implementing additive manufacturing processes include the University of Arizona, University of Virginia and University of Colorado – Boulder.
If you are interested in learning more about the increasingly vital role additive manufacturing plays in the hypersonics industry, be sure to register for IDGA’s Hypersonic Weapons Summit this September 17-18 at The Bethesda Marriot in Maryland.